La minera inició su producción comercial a mediados del 2015. Sus operaciones mineras se localizan en la II de Región Antofagasta, comuna de Sierra Gorda, a 170 kilómetros de Antofagasta, 4,5 kilómetros de Sierra Gorda y a una altura de 1.626 m.s.n.m.
La empresa nace de un proyecto conjunto (Joint Venture) entre la compañía polaca KGHM Polska Miedz S.A., a través de su subsidiaria KGHMI (55%), y las japonesas Sumitomo Metal Mining (31,5%) y Sumitomo Corporation (13,5%).
Pioneros en minería de baja ley
La mina Sierra Gorda explota un yacimiento de óxidos y sulfuros de cobre; y molibdeno, como subproducto. Es la operación que produce con menor ley de sulfuros de cobre, de alrededor de 0,3%.
Se trata de una explotación a cielo abierto, con procesos de extracción mediante explosivos, equipos de carguío y camiones de transporte de mineral a la planta de procesamiento donde el mineral es triturado y molido, con un rendimiento medio equivalente a 115.000 toneladas de mineral diarias.
Para el proceso de flotación se emplea la instalación de separación del concentrado de molibdeno del cobre, que deriva en una producción de 550.000 toneladas de concentrado de cobre al año.
El 2020, la producción de la minera alcanzó las 156.115 toneladas de cobre fino y 7.614 toneladas de molibdeno, siendo un importante aporte a la producción del país.
La producción de concentrado de cobre se transporta, entre otros destinos, al puerto de Antofagasta y de allí se envía vía marítima a plantas metalúrgicas de todo el mundo.
Procesos mineros
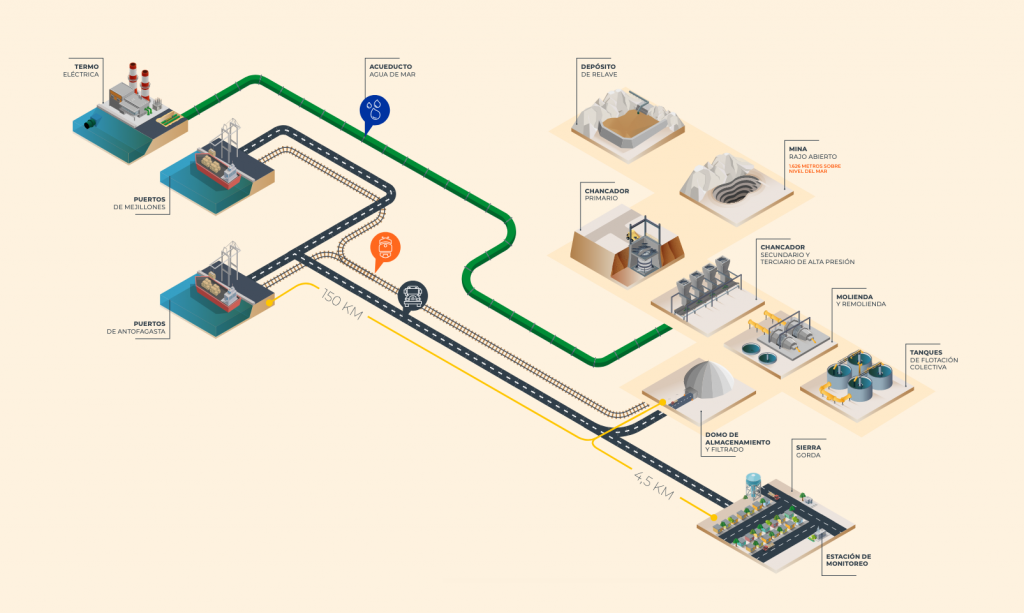
Procesos planta de sulfuros
Chancado primario
Los camiones CAEX de extracción transportan el mineral desde la mina y desde el acopio de mineral sulfurado, descargando en una línea de chancadores giratorios, que poseen sistemas de supresión y colectores de polvo.
Mediante correas transportadoras, el material chancado se descarga en el acopio de mineral grueso. Las correas tienen un electromagneto que captura las partes metálicas, evitando daños en las correas y la línea de procesos aguas abajo.
Acopio mineral grueso
Chancado secundario y terciario
La correa de descarga del acopio conduce el mineral grueso hacia un sistema de harneros secundarios vibradores, que remueve el mineral (menor a 2 pulgadas de diámetro) y que es conducido al acopio de molinos de rodillo de alta presión (HPGR – High Pressure Grinding Rolls).
El mineral de sobretamaño va directamente al chancador secundario de cono.
El mineral grueso proveniente del chancador giratorio pasa por un sistema de cuatro chancadores secundarios de cono, configurados para entregar un material con una granulometría de 36 mm. Actualmente se han instalado cuatro de estos chancadores secundarios de cono, quedando el espacio disponible para instalar los tres chancadores restantes.
El material que no alcanza la granulometría requerida para el proceso será enviado a la etapa de chancado terciario, que incluye siete chancadores de guijarros (pebbles), de los que hay instalados cuatro.
Tanto los harneros como los chancadores de cono y HPGR cuentan con sistemas colectores de polvo.
Molienda
Las partículas suficientemente finas se envían al primer proceso de flotación (celdas Rougher), mientras que la fracción gruesa vuelve al molino de bolas.
En el circuito de molinos de bola, cada molino opera con su propio grupo de ciclones y cajas de bombeo de descarga. Los molinos están controlados por un sistema de control distribuido y un sistema de supervisión, que permiten controlar las tasas de tonelaje y tamaño del material.
En la planta actualmente operativa, se han instalado dos de los tres molinos considerados originalmente.
Chancado secundario y terciario
La concentración de los minerales se realiza mediante flotación en el cual se inyecta aire y reactivos químicos que permiten que la fracción del mineral que contiene cobre se adhiera a las burbujas de aire, flote y pueda ser removido. El circuito de flotación contempla las siguientes etapas:
- La flotación primaria (Rougher), en la cual se agrega una lechada de cal a la pulpa proveniente de la molienda de tal forma de aumentar el pH y descartar el material sin valor económico (relave).
- La flotación de limpieza y scavenger producen concentrado de cobre y de molibdeno, con un alto nivel de recuperación del metal.
Flotación selectiva
Para la separación del concentrado de cobre del concentrado de molibdeno se realiza la flotación selectiva y se agregan los reactivos necesarios para producir dicha separación.
Por medio de canaletas, la cola de la flotación primaria del concentrado de cobre es conducida directamente hacia los espesadores.
En tanto, el concentrado de molibdeno es conducido por cañerías hasta el cajón de impulsión hacia etapas de flotación de limpieza.
Espesamiento concentrado de molibdeno
Espesamiento y filtrado concentrado de cobre
Actualmente, el concentrado de cobre es espesado y luego enviado a una planta de filtrado (con tres filtros prensa).
El concentrado es enviado a un galpón de almacenamiento con capacidad de 80 mil toneladas para los primeros cuatro años de operación. Esta instalación se ampliará posteriormente a 120 mil toneladas para el resto del periodo de operación.
Este acopio cerrado se ubica al lado del sistema de carguío de concentrados en vagones de tren y de camiones.
Espesamiento de relaves
Cada espesador cuenta con dos bombas, cada una con motores de 485 kW y variador de frecuencia, que bombean los relaves al cajón colector de relaves existente, desde donde comienza el sistema de conducción hasta el depósito de relaves.
Los relaves son espesados hasta alcanzar una concentración de sólidos entre 55 a 60 %.
Depósito de relaves
Los relaves del proceso de flotación son transportados a través de un sistema de conducción gravitacional, que tiene una tubería permanente y otra de emergencia, ambas de HDPE.
Los relaves se dirigen hacia el depósito de relaves, que tiene una superficie de 2.315 hectáreas, con una capacidad de mil millones de m3 de relaves y 95 metros la altura del muro principal. . El sistema parte desde un cajón inicial de disipación de energía.